Wer schon mal mit Legosteinen* gebaut hat, weiß, dass gutes Vorabsortieren und Bereitlegen der Steine entscheidend zum erfolgreichen Bauen beitragen. Die langwierige Sucherei nach dem passenden Stein entfällt, das Erfolgserlebnis folgt prompt. Bei Maschinen, die etwas zusammenbauen sollen, seien es Autos oder wie in unserem Fall Insulin-Pens, ist das nicht anders. Sie wollen die Bauteile zwar nicht unbedingt auf dem sprichwörtlichen Silbertablett geliefert bekommen, aber sie sollen vorsortiert und in festgelegtem Abstand voneinander präsentiert werden, so dass die vollautomatisierten Maschinen sie problemlos greifen und in den Montageanlagen verarbeiten können.
Damit das funktioniert, benutzt man bei Sanofi in der Pen-Fertigung rechteckige Transportkisten, in die, sauber aufgereiht, jeweils knapp 200 Einzelteile passen. Diese Transportkisten, von Fachleuten Tray genannt, sind also quasi das Silbertablett, auf dem die Bauteile serviert werden. Hergestellt werden sie unter anderem bei dem finnischen Unternehmen Satatuote Oy, einem Spezialisten für Verpackungslösungen aus Kunststoff für Pharmaprodukte sowie Medizintechnik. Die Trays bestehen aus Polystyrol (PS), einem hochwertigen Standardkunststoff, von dem in ganz Deutschland jährlich gut 725.000 Tonnen verbraucht werden - das sind gut fünf Prozent der gesamten hierzulande verbrauchten Kunststoffmenge1. Das Herstellungsprinzip der Trays ist einfach: Da Polystyrol ein Thermoplast ist, also bei Raumtemperatur hart, bei erhöhter Temperatur dagegen verformbar ist, kann eine dünne Polystyrolfolie erwärmt und in eine vorgefertigte Negativform gepresst werden. Nach dem Abkühlen sind die Trays fertig, werden zu den Herstellern der Bauteile geliefert, dort bestückt und kommen dann zur Endverarbeitung zu Sanofi.
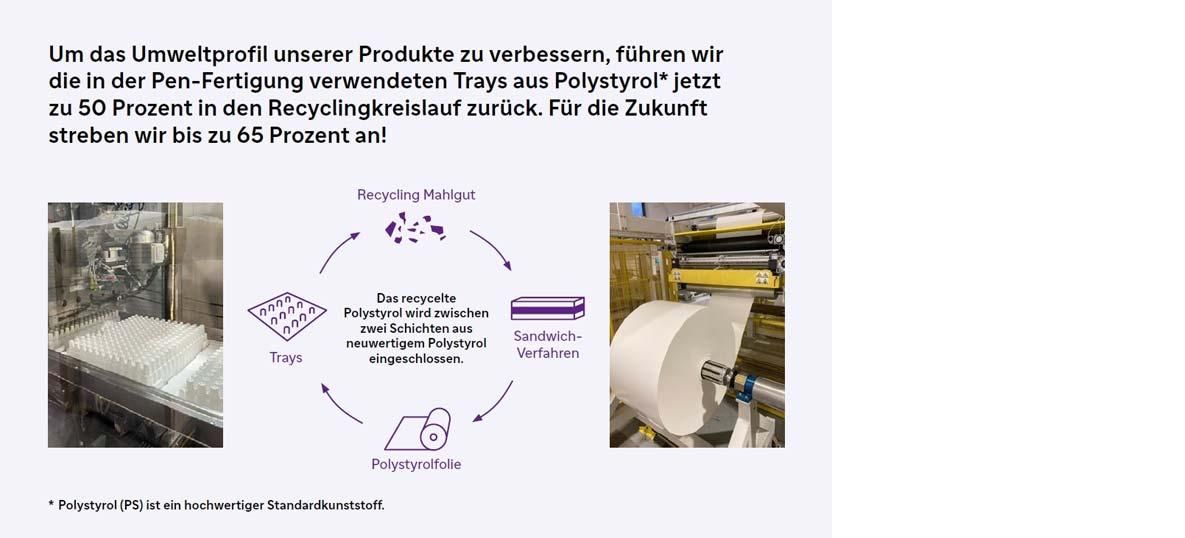
Nun hat so ein Kunststoff, hergestellt aus Erdöl, logischerweise auch einen ökologischen Fußabdruck. Bei Polstyrol liegt er bei 3,8 Kilogramm CO2eq pro Kilogramm2,3. Was also liegt näher, als möglichst viel Polystyrol einzusparen? Schließlich ist der Kunststoff in purer Form gut recycelbar. Oder man könnte die Trays wiederverwenden – was leider bei der Pen-Produktion aus Gründen der pharmazeutischen Qualitätssicherung nur bedingt funktioniert. Ein großer Teil der Trays kann ein zweites Mal verwendet werden. Um die Wertschöpfung zu erhöhen, bietet es sich also an, sie zu recyceln. Dazu werden die Trays zerkleinert; das daraus entstandene Mahlgut kann dann erneut aufgeschmolzen und weiterverarbeitet werden. Bisher hat das Recyclingunternehmen das Mahlgut direkt auf dem Markt für Sekundärrohstoffe verkauft. Das hat Sanofi jetzt geändert und führt einen Teil des verwendeten Polystyrols im Kreis, indem das Mahlgut direkt wieder an den Tray-Hersteller Satatuote Oy geht. Der Trick ist, dass der recycelte Rohstoff in den dünnen Polystyrolfolien wie bei einem Sandwich zwischen zwei Schichten neuwertigem Rohstoff liegt. Denn ausschließlich recyceltes Polystyrol darf bisher aus Qualitätsgründen nicht zur Herstellung für Pharmaprodukte verwendet werden. Die zur Tray-Herstellung verwendete Polystyrolfolie hat also drei Schichten in unterschiedlichen Dicken, jeweils außen „frisches“ Polystyrol, in der Mitte das Recyclingprodukt. Damit schließt sich der Kreis und 50 Prozent des Polystyrols werden im Kreis geführt. Zudem werden im Vergleich zum bisherigen Prozess 1.058 Tonnen CO2eq vermieden und 5.000 Kubikmeter weniger Frischwasser verbraucht. Das seit Ende 2022 kontinuierlich laufende Projekt trägt also maßgeblich dazu bei, Medizinprodukte wie die Insulin-Pens nachhaltiger zu machen, und ist damit ein wichtiger Baustein unserer Nachhaltigkeitsstrategie. „Planet Care” bedeutet für uns vor allem den sorgsamen Umgang mit natürlichen Ressourcen. „Zudem ist das Projekt auch ökonomisch sinnvoll, schließlich müssen sich die Dinge rechnen, sonst setzen sie sich auf Dauer nicht durch“, betont Anne Reuschenbach, die bei Sanofi den Bereich Pharmazeutische Produktion und Fertigung von Sanofi in Deutschland in der Geschäftsführung verantwortet. „Durch das Recycling müssen wir erheblich weniger für Rohstoffe bezahlen. Ein einziges Tray kostet deutlich weniger – bei 2,5 Millionen Trays pro Jahr rechnet sich das!“ ergänzen Hendrik Hoppe und Frank Bien, Ideenentwickler und zuständige Projektleiter von Sanofi Deutschland nicht ohne Stolz.
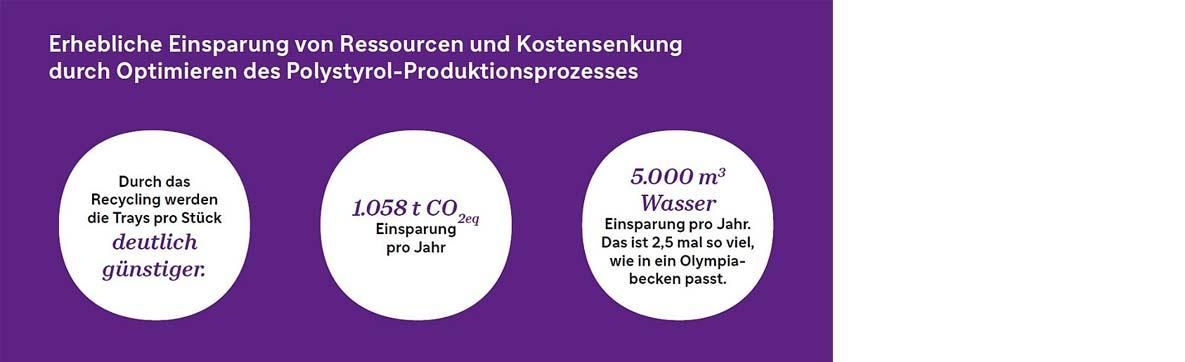
Quellen
1 https://www.umweltbundesamt.de/daten/ressourcen-abfall/verwertung-entsorgung-ausgewaehlter-abfallarten/kunststoffabfaelle#kunststoffvielfalt
2 https://www.studiofreudigmann.com/blogs/magazin/co2-fussabdruck
3 BAFA, Informationsblatt CO2-Faktoren, 11/2021, pdf-Datei abrufbar bei www.bafa.de
*LEGO® ist eine Marke der LEGO Gruppe.